Article publié le 15 janvier 2025 sur 3DNatives.com par Mélanie W.
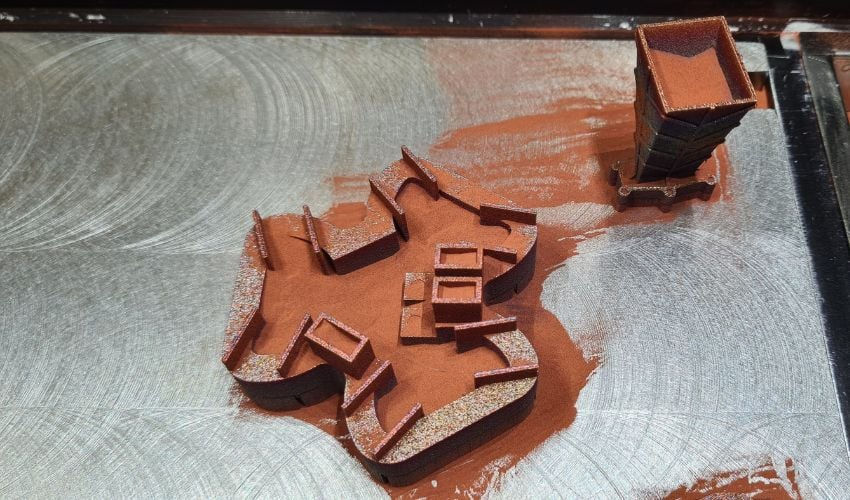
AFU, entreprise française spécialisée dans l’usinage, a investi dans l’impression 3D métal depuis 2014 pour élargir ses capacités et produire des composants plus complexes. Aujourd’hui équipée de 3 machines, elle a travaillé pendant deux ans sur la paramétrie du cuivre, et plus particulièrement sur l’alliage de cuivre-chrome-zirconium (CuCrZr). L’objectif était de pouvoir imprimer en 3D des pièces en cuivre avec une excellente densité tout en conservant ses propriétés intrinsèques, le tout sur une machine standard, équipée d’un laser infrarouge de 400W. Un défi qu’elle a su relever puisqu’elle est en mesure de fabriquer des pièces denses (>99,5%), avec une épaisseur de couche de 40 microns, depuis l’été 2024, ce qui est une première en France.
Basée à Saint-Malo, l’entreprise AFU accompagne depuis de nombreuses années ses clients industriels, issus de différents secteurs d’activité dans la réalisation de leurs projets. En 2014, elle s’est tournée vers la fabrication additive métal, et plus particulièrement vers la fusion laser sur lit de poudre (L-PBF / SLM), afin de proposer des pièces plus complexes, sur-mesure ou encore des prototypes en un temps record. L’entreprise offre une large gamme de métaux, dont le cuivre, réputé pour ses propriétés thermiques et électriques. Toutefois ces dernières sont aussi les raisons pour lesquelles le cuivre sous forme de poudre est plus difficile à imprimer que d’autres métaux comme le titane, l’aluminium ou l’acier.
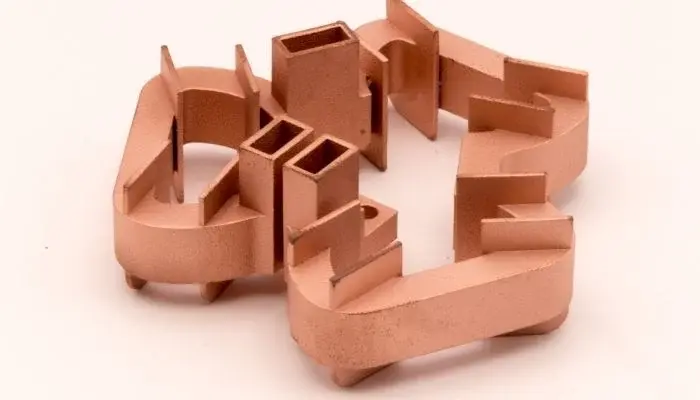
Le cuivre en fabrication additive
Le marché de la fabrication additive a vu ces dernières années de nombreux développements autour du cuivre, un métal particulièrement apprécié pour sa conductivité, sa ductilité, sa résistance à l’usure ou encore à la corrosion. Il est donc idéal pour des applications dans l’aérospatiale et l’électronique, la fabrication d’échangeurs thermiques ou d’inducteurs, etc. Cependant, le cuivre n’est pas un métal facile à imprimer, surtout quand on utilise une machine qui emploie un laser infrarouge comme c’est le cas sur la plupart des solutions de fusion laser.
Le cuivre dissipe en effet une partie de l’énergie du laser, engendrant alors une perte importante de puissance ce qui ne permet pas de réaliser une fusion optimale. Avec un laser infrarouge d’une puissance de 200W ou 400W – ce qui correspond à la majorité des solutions métalliques du marché – la fusion n’est pas totale ce qui crée des zones fragiles, une porosité trop élevée et une conductivité trop basse. Concrètement, il faudrait utiliser 100 % de la puissance du laser pour obtenir des résultats satisfaisants et une bonne densité. Or, 60 % de l’énergie transmise au matériau est perdue (dissipée par la poudre ou réfléchie lors de la fusion). On comprend donc qu’avec un laser d’une telle puissance et sans développement spécifique, on ne peut pas compenser les pertes et les pièces obtenues seront poreuses.
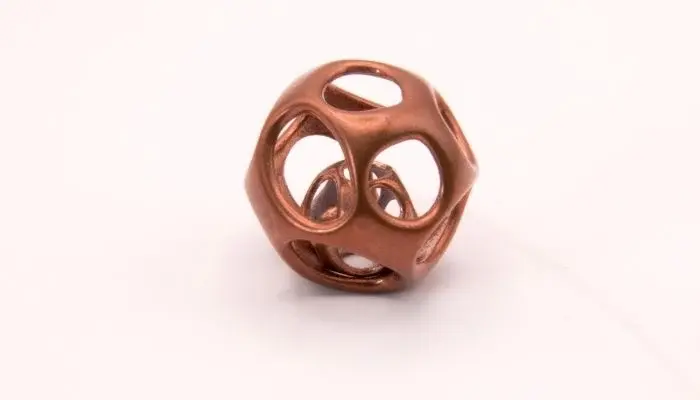
Comment palier ce défi ?
L’une des premières solutions serait d’utiliser une machine avec un laser plus puissant, de 1kW par exemple. Elles existent sur le marché mais sont très chères et demandent des investissements supplémentaires en termes d’infrastructure pour les accueillir.
L’autre option est d’opter pour un laser vert qui offre un taux d’absorption par le cuivre beaucoup plus important qu’un laser infrarouge. Ainsi, les pièces obtenues présentent de meilleures propriétés et la paramétrie est plus facile à déterminer. Toutefois, les machines équipées d’un tel laser sont encore rares, chères et souvent limitées en termes de taille de volume d’impression.
Enfin, certains acteurs du marché se sont penchés sur la composition même du cuivre. En appliquant un revêtement sur les particules de cuivre, comme du graphène, il serait possible d’améliorer l’absorption de l’énergie. Cependant, cela vient altérer les propriétés thermiques et électrique du métal, ce qui est potentiellement problématique pour la réalisation des pièces souhaitées.
Il semblerait donc que les possibilités pour surmonter les défis liés à l’impression de cuivre avec une machine laser de 400W soient limitées. Face à ce constat, AFU a mené des travaux de recherche pendant deux ans afin de trouver la paramétrie idéale pour utiliser l’alliage CuCrZr sur une imprimante 3D EOS M290 400W.

L’impression de cuivre par AFU
Après avoir investi dans une nouvelle machine métal en 2021, une EOS M290 400W, AFU a démarré des tests avec du cuivre pur. Si les pièces de démonstration réalisées étaient satisfaisantes, présentant un bon état de surface et une bonne précision dimensionnelle, les composants intégrant des canalisations n’ont pas donné les mêmes résultats. En effet, les examens métallographiques ont montré toutes les limites citées ci-dessus. Trop de porosités ont été constatées ce qui ne permettait pas de fabriquer des pièces étanches à l’eau. Est-il finalement possible d’imprimer du cuivre avec de bonnes propriétés sur une machine de 400W avec un laser infrarouge ?
AFU commence alors à tester une machine de 1kW et caractérise plusieurs pièces réalisées en CuCp (Cuivre Commercialement Pur) 40µm Standard. La densité est bien meilleure et les résultats sont satisfaisants. Toutefois, investir dans une telle solution représentait un coût trop élevé pour l’entreprise française. Elle s’est alors posé la question de la paramétrie de sa machine actuelle et s’est lancée dans des travaux pour trouver le bon équilibre entre les différents paramètres.
Quatre facteurs influent directement la fusion du cuivre en fabrication additive : l’épaisseur de couche, la vitesse de balayage du laser, la puissance de celui-ci et l’écart entre le vecteur. L’équilibre entre ces quatre paramètres est plus difficile à trouver que pour d’autres métaux tels que le titane TA6V ou l’AlSi10Mg.

AFU mène alors plusieurs recherches sur la granulométrie, la composition chimique des poudres utilisées, sur le comportement du matériau à la mise en œuvre par fusion laser, sur les fournisseurs de poudre pour la fabrication additive, etc. De nombreux essais ont été menés, selon des exigences de contrôle en laboratoire très précises (contrôle de la densité apparente et tassée de la poudre, de la composition chimique de la poudre, de la granulométrie de la poudre, de la composition chimique de la pièce, de la traction et conductivité électrique). Deux épaisseurs de couches de fabrication ont été testées – 20 et 40 microns – avec deux fournisseurs de poudre différents.
Après plusieurs impressions, AFU a atteint les résultats souhaités sur sa machine de 400W. Elle explique : “Nous sommes en mesure de produire des pièces étanches, avec des propriétés métallurgiques équivalentes au CuCrZr disponible en barre, plaques, fil… avec un process stable et répétable. Nous sommes les seuls en France à le faire sur une machine standard et en 40µm. Le CuCrZr disponible sur EOS M400 1kW est exclusivement en 80µm par exemple.”
Les travaux menés par AFU sont incontestablement innovants, offrant des solutions aux défis rencontrés dans la fabrication additive du cuivre. L’été dernier, l’entreprise française a franchi une étape décisive en produisant avec succès ses premières pièces destinées aux clients. Si vous êtes intéressés par ses recherches ou que vous avez un projet d’impression 3D de cuivre, n’hésitez pas à cliquer ICI et à contacter leurs équipes.
Que pensez-vous des réalisations de l’entreprise française AFU ? N’hésitez pas à partager votre avis dans les commentaires de l’article. Retrouvez toutes nos vidéos sur notre chaîne YouTube ou suivez-nous sur Facebook ou LinkedIn !
*Crédits de toutes les photos : AFU
コメント